I am a reloader from 1978 or so and swager from 1982. I guess cost to me was always relative, while in the business of making bullets for demanding customers the best tools were necessary... While I did sell most of my equipment I did cherry pick a good selectionof manual tools and a few caliber choices to continue as a hobby.
I can tell you without any reservations that it is much better as a hobby rather than a profession. I also note that reloading in general and casting (I still do some casting, but prefer jacketed bullets) and particularly swaging are rare, not particularly for saving money (yet that seems to be an issue again now) and appeals to a narrow personality type (my wife would call it a disorder). I am about the youngest swaging loader I know of (not 50 for some time yet).
As luck would have it swaging is not that hard to get into if you plan to swage small caliber or pistol bullets (lead or jacketed) as there are “reloading press” swage dies. Although I use a large array of expensive dies I have lots of respect for the CH/4D effort to keep home swaging dies within reason (cost) along with the limited selection of reloading press dies available from Corbin or RCE/Walnut Hill.
Honestly I loved reloading so much that I accidentally got into swaging when I was taking a hunter education course. The older gentleman who was teaching the class was an old buddy of my grandfathers and he had an old swage set from Ted Smith that would do jacketed and 3/4 .357...
I was hooked and then saved up to get my first M style press (I still have it) and started with .224 and then .308 then 9mm, .357 and on.
Swaging like reloading is for the most part not for saving money but rather doing something others cannot produce. A nice thing about making .224 bullets (what the .223/5.56 uses) with old .22 shells is the thin jacket great for varmint shooting, the .22 LR makes a particullarly thin jacket and the FPS that thin jacket can take is almost maxed out with the .223/5.56. For shooting pests and non fur gathering coyote shooting you can't beat a frangable .223 with a thin jacket .22 lr conversion, the bullets are often ugly and great care must be taken not to fold the jacket over (heat-treating helps) - so to make the point again, money savings is killed by the higher labor/time nessassary.
Looking over the Corbin website I was checkig the .22 lr conversion dies (work with a reloading press) to iron out the rim on a .22lr is $130 then you could add the reloading die type set to seat the core and form the point that set is $348.00. That is a 2-die set for .224 cal and makes an 6-S ogive. 6s is a standard ogive, a middle of the road point curve with 3-5 good for heavy hunting bullets with a more rounded nose and 8 plus reserved for target/long range shooting. When I got my first set of conversion dies I jumped full in and got dies and the special press along with the reloading press dies for ironing out the .22 lr rims... the entire set cost less than the above together...
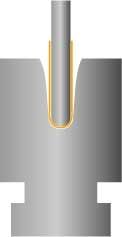
My first MM style press was the "gold" series press (the shortest run ever made) cast from an industrial non spark bronze (and gave it the gold color - now with a nice patina green/brown/gold). If you wanted to cut lead wire or cast cores to weight and seat the core or use "sand shot" to make frangable cores the reloading dies work well as long as you have a good strong press like the Lee Classic Cast Press, RCBS Rock Chucker Supreme (both minumum), or the CH4D Heavy Duty Champion Press. I would not recomend any speciality press or turret press for this operation.
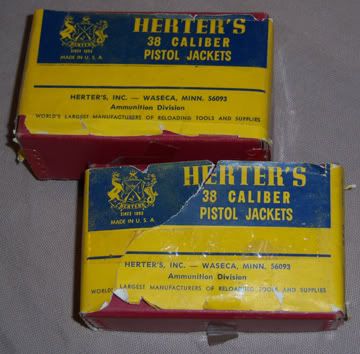
Just to be fair CH4D also makes dies for swaging, but most are made for jacketed pistol bullets, the dies are based on some of the older Herters reloading die thread type of dies. That CH4D press is also a great monster reloading press! For swaging I prefer the Corbin or Walnut hill type press (can double as a super heavy reloading press). The CH/4D dies also require a mallet or a drag-down frame that pushes out the bullet when you return the handle on the press.
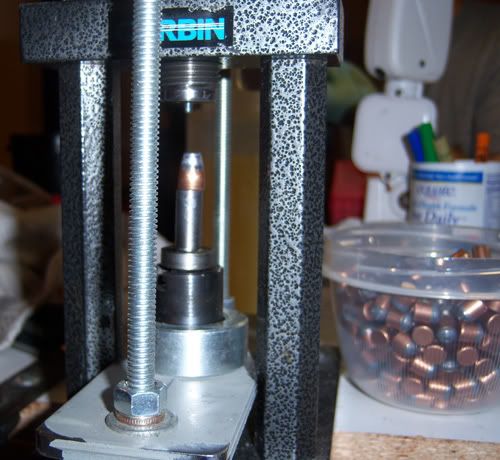
The Corbin press with the CH/4D dies and the ejector frame device attached (the threaded posts)
When I ran the business I had a knack for creative bullet design and sold to a specific group of markets - Benchrest, Varmint shooters, and Special demands... All three markets, at least for me represented a demand for frangible bullets (come apart on impact, one of the most popular was a low penetration frangible that had a lower chance of deep penetration in walls and was very good at breaking glass windows without having large heavy parts continue to go past the glass - that was a very special use bullet. Now I make jacketed bullets for my own use, I make just regular lead core target bullets, bonded lead core bullets for hunting, and frangible bullets for shooting coyote (pest removal, as frangible tends to ruin the pelt and I like to use .308 for coyote frangible in .308 would not leave enough pelt to make it worth the work).
I have even produced powder tungsten core bullets for special applications by custom order, but the material is too expensive for general use. I never bothered to make or even atempt much with solid gliding metal or copper bullets because the need for higher level hydraulic equipment was never worth the investment in light of the market availability of higher production run products (like Barnes).
If a a budget is the issue.... I was looking at the RCE site for reloading dies, it seems Richard wanted to make available swage equipment for reloading in a mass-market way to keep the prices down and have items in stock... Both Corbin brothers are notoriously behind in production and rarely have much in stock a crop of new producers are springing up and this is GREAT news. BTSniper Custom Tools and Dies is one such producer.
Prices are lower, and the .22lr dies for the conversion are listed at (Rimfire jacket maker .224 caliber RFJ224-1) $60.00 not a bad price... The two die set for making jacketed bullets (pre cut and weighed core -no core swage (that takes the larger special presses) is listed at (22 .224” Flat base, 6S TOS224-1) $175.00.
So the total with a bottle of lube (this is important - lube and the properuse is one of the keys nessassary) would be about $240.00 for .224 jacketed bullets (not counting lead wire or cast cores) using a good pre existing reloading press ...
Not bad, as far as cost. $240. (Note: prices are now out of date and products may be unavailable)
I though a few would like a simple overview of the swage process with some drawings I made...
The drawings are deliberately exaggerated to explain the process...
The process is based on making cold flow lead swaged jacketed bullets, other materials take a different procedure. The Drawings are also based on the special equipment I have that is designed only for swaging, the reloading press dies work in a similar way but not in the exact same way and also have fewer steps... Swaging is a process of expanding up not squeezing down in diameter, a smaller thinner (but taller) product is expanded under pressure to fill a larger diameter...
Step one.
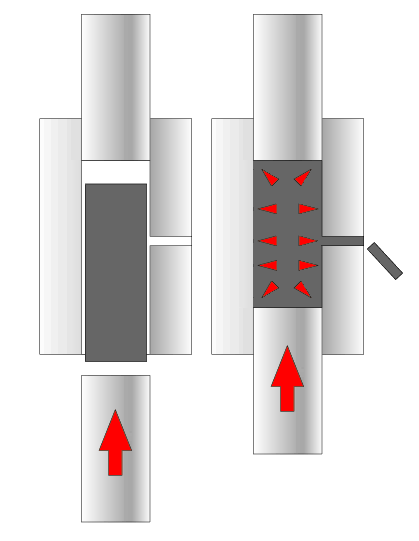
You need a lead core to place in the jacket...
If you are using the reloading type dyes the core is made of pre cast lead or cut lead wire and filed or whittled to the correct weight. If you are using die sets that contain a core swage then this the first step is to cut a lead wire just slightly heavier than needed. Take the cut wire and place it into the core swage, pull down on the press handle and apply pressure to the lead until it fills the die and starts to squeeze out of the bleed hole, once adjusted the core swage will make all of the cores the exact same weight and size. Proper pressure resistant lubrication (I use a lanolin/castor oil based lubrication) is applied to the lead before forming or the core will get stuck. The lubrication must be removed with a solvent like alcohol before the next step.
Second step.
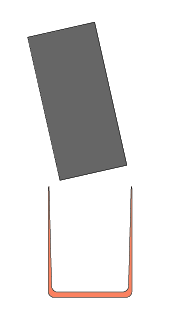
The second step (or first step for reloading press dies) is to place the clean, weighted core into the jacket ready for the core seat die.
Third step.
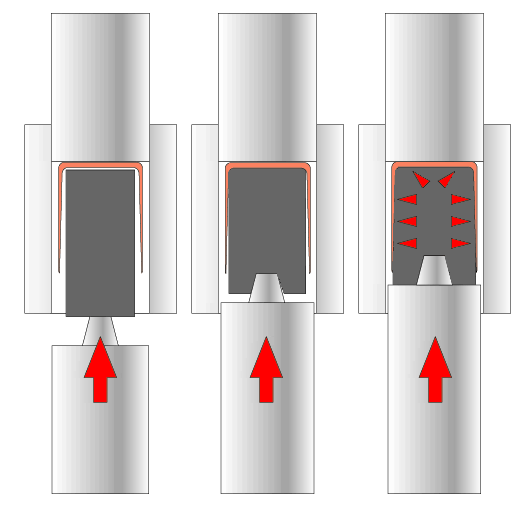
This step is where the core is expanded into the jacket, note that the core when compressed will flow around the punch (and in this case the hollow point is pressed into the lead) until the expansion is stopped by the jacket as it is pressed against the inside of the die.
Note that this punch is made slightly smaller than the inside of the die to fit INTO the jacket to produce a true hollow point with an ogive (curved part of the front) that is covered by the jacket.
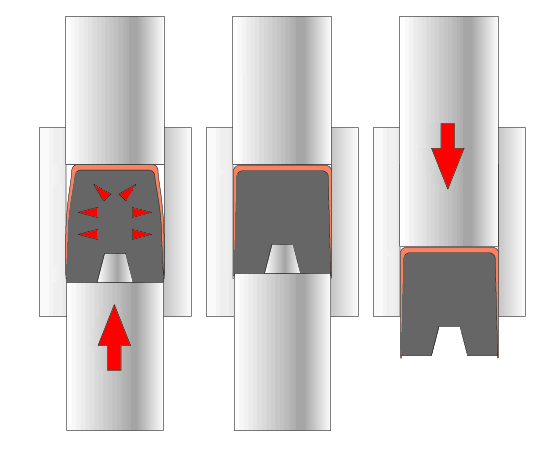
Note that as the punch comes to it's final position the jacket has expanded to the inside of the die with a hard pressed lead core on the inside. As before proper lubrication is necessary or the lead seated into the jacket will lock the jacket into the die, lubrication only on the outside of the jacket.
Once fully seated the jacket and core is ejected from the die.
Fourth step.
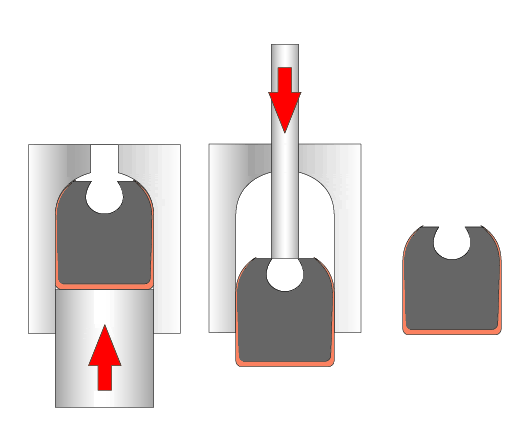
The last step in making this jacketed bullet is to form the point or ogive.
Using the ogive or point forming die, the seated core is placed into the die and will form a point and slightly expand as pressure is applied.
The hollow point is forming under the jacket as the ogive is folded over the open lead.
Once formed the final finished bullet is ejected by a punch.
It takes longer to read that than to do each step...
About the time and force of forming .357 cases and seating a bullet...
For reloading die type swage dies... CH4D
Look under "bullets" from the left hand list...
Go to 101 bullet swage dies...
This is a two step swage die (no core swage) for a jacketed HP...
101410HP 10mm/40 S&W Hollow Point Swaging Die Set - $ 185
Or the soft poont...
101410SP 10mm/40 S&W Soft Point Swaging Die Set - $ 185
The folks at CH4D are great, I have used their "speciality die" custom services before and were great to work with, they make a great product...
The dies they use are the older style Ted Smith type for reloading presses and they can be broken if not uses correctly (in fact all dies can be cracked when using the wrong lead it must be the lead hardness it was designed for harder lead larger holes).
A part of RCE, makes dies for reloading presses...
They also make the special dies for the swage presses (like I use).
I will post more on the CH4D dies and my .355 hollow point set I have.
I can tell you without any reservations that it is much better as a hobby rather than a profession. I also note that reloading in general and casting (I still do some casting, but prefer jacketed bullets) and particularly swaging are rare, not particularly for saving money (yet that seems to be an issue again now) and appeals to a narrow personality type (my wife would call it a disorder). I am about the youngest swaging loader I know of (not 50 for some time yet).
As luck would have it swaging is not that hard to get into if you plan to swage small caliber or pistol bullets (lead or jacketed) as there are “reloading press” swage dies. Although I use a large array of expensive dies I have lots of respect for the CH/4D effort to keep home swaging dies within reason (cost) along with the limited selection of reloading press dies available from Corbin or RCE/Walnut Hill.
Honestly I loved reloading so much that I accidentally got into swaging when I was taking a hunter education course. The older gentleman who was teaching the class was an old buddy of my grandfathers and he had an old swage set from Ted Smith that would do jacketed and 3/4 .357...
I was hooked and then saved up to get my first M style press (I still have it) and started with .224 and then .308 then 9mm, .357 and on.
Swaging like reloading is for the most part not for saving money but rather doing something others cannot produce. A nice thing about making .224 bullets (what the .223/5.56 uses) with old .22 shells is the thin jacket great for varmint shooting, the .22 LR makes a particullarly thin jacket and the FPS that thin jacket can take is almost maxed out with the .223/5.56. For shooting pests and non fur gathering coyote shooting you can't beat a frangable .223 with a thin jacket .22 lr conversion, the bullets are often ugly and great care must be taken not to fold the jacket over (heat-treating helps) - so to make the point again, money savings is killed by the higher labor/time nessassary.
Looking over the Corbin website I was checkig the .22 lr conversion dies (work with a reloading press) to iron out the rim on a .22lr is $130 then you could add the reloading die type set to seat the core and form the point that set is $348.00. That is a 2-die set for .224 cal and makes an 6-S ogive. 6s is a standard ogive, a middle of the road point curve with 3-5 good for heavy hunting bullets with a more rounded nose and 8 plus reserved for target/long range shooting. When I got my first set of conversion dies I jumped full in and got dies and the special press along with the reloading press dies for ironing out the .22 lr rims... the entire set cost less than the above together...
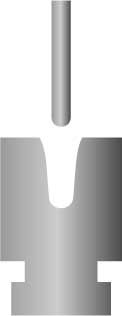
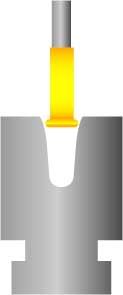
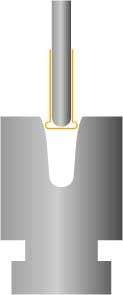
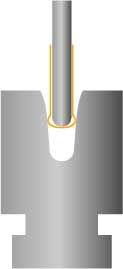
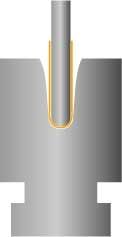
My first MM style press was the "gold" series press (the shortest run ever made) cast from an industrial non spark bronze (and gave it the gold color - now with a nice patina green/brown/gold). If you wanted to cut lead wire or cast cores to weight and seat the core or use "sand shot" to make frangable cores the reloading dies work well as long as you have a good strong press like the Lee Classic Cast Press, RCBS Rock Chucker Supreme (both minumum), or the CH4D Heavy Duty Champion Press. I would not recomend any speciality press or turret press for this operation.
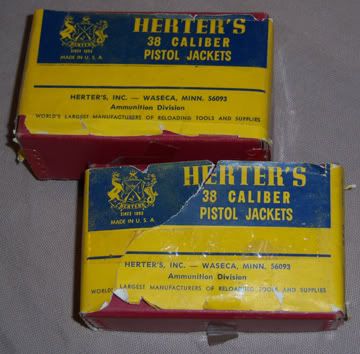
Just to be fair CH4D also makes dies for swaging, but most are made for jacketed pistol bullets, the dies are based on some of the older Herters reloading die thread type of dies. That CH4D press is also a great monster reloading press! For swaging I prefer the Corbin or Walnut hill type press (can double as a super heavy reloading press). The CH/4D dies also require a mallet or a drag-down frame that pushes out the bullet when you return the handle on the press.
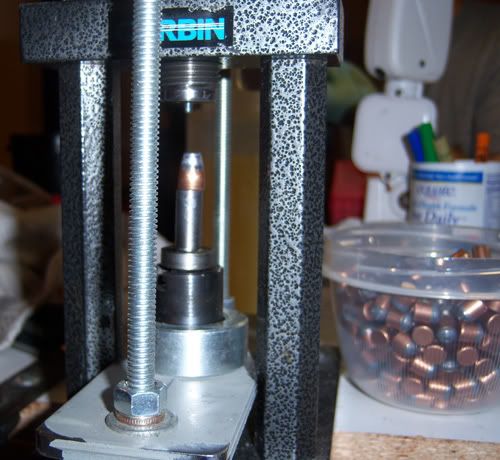
The Corbin press with the CH/4D dies and the ejector frame device attached (the threaded posts)
When I ran the business I had a knack for creative bullet design and sold to a specific group of markets - Benchrest, Varmint shooters, and Special demands... All three markets, at least for me represented a demand for frangible bullets (come apart on impact, one of the most popular was a low penetration frangible that had a lower chance of deep penetration in walls and was very good at breaking glass windows without having large heavy parts continue to go past the glass - that was a very special use bullet. Now I make jacketed bullets for my own use, I make just regular lead core target bullets, bonded lead core bullets for hunting, and frangible bullets for shooting coyote (pest removal, as frangible tends to ruin the pelt and I like to use .308 for coyote frangible in .308 would not leave enough pelt to make it worth the work).
I have even produced powder tungsten core bullets for special applications by custom order, but the material is too expensive for general use. I never bothered to make or even atempt much with solid gliding metal or copper bullets because the need for higher level hydraulic equipment was never worth the investment in light of the market availability of higher production run products (like Barnes).
If a a budget is the issue.... I was looking at the RCE site for reloading dies, it seems Richard wanted to make available swage equipment for reloading in a mass-market way to keep the prices down and have items in stock... Both Corbin brothers are notoriously behind in production and rarely have much in stock a crop of new producers are springing up and this is GREAT news. BTSniper Custom Tools and Dies is one such producer.
Prices are lower, and the .22lr dies for the conversion are listed at (Rimfire jacket maker .224 caliber RFJ224-1) $60.00 not a bad price... The two die set for making jacketed bullets (pre cut and weighed core -no core swage (that takes the larger special presses) is listed at (22 .224” Flat base, 6S TOS224-1) $175.00.
So the total with a bottle of lube (this is important - lube and the properuse is one of the keys nessassary) would be about $240.00 for .224 jacketed bullets (not counting lead wire or cast cores) using a good pre existing reloading press ...
Not bad, as far as cost. $240. (Note: prices are now out of date and products may be unavailable)
I though a few would like a simple overview of the swage process with some drawings I made...
The drawings are deliberately exaggerated to explain the process...
The process is based on making cold flow lead swaged jacketed bullets, other materials take a different procedure. The Drawings are also based on the special equipment I have that is designed only for swaging, the reloading press dies work in a similar way but not in the exact same way and also have fewer steps... Swaging is a process of expanding up not squeezing down in diameter, a smaller thinner (but taller) product is expanded under pressure to fill a larger diameter...
Step one.
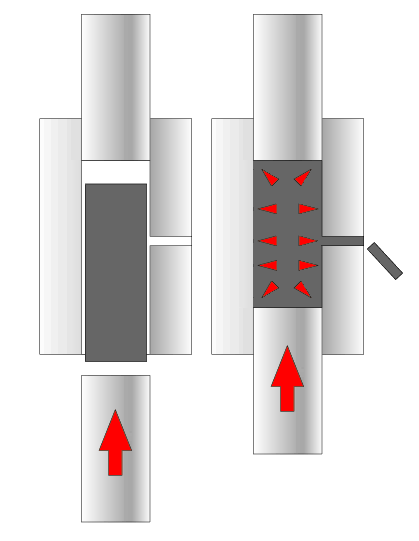
You need a lead core to place in the jacket...
If you are using the reloading type dyes the core is made of pre cast lead or cut lead wire and filed or whittled to the correct weight. If you are using die sets that contain a core swage then this the first step is to cut a lead wire just slightly heavier than needed. Take the cut wire and place it into the core swage, pull down on the press handle and apply pressure to the lead until it fills the die and starts to squeeze out of the bleed hole, once adjusted the core swage will make all of the cores the exact same weight and size. Proper pressure resistant lubrication (I use a lanolin/castor oil based lubrication) is applied to the lead before forming or the core will get stuck. The lubrication must be removed with a solvent like alcohol before the next step.
Second step.
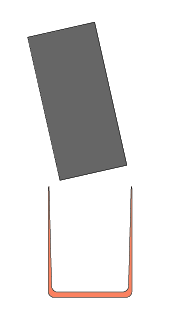
The second step (or first step for reloading press dies) is to place the clean, weighted core into the jacket ready for the core seat die.
Third step.
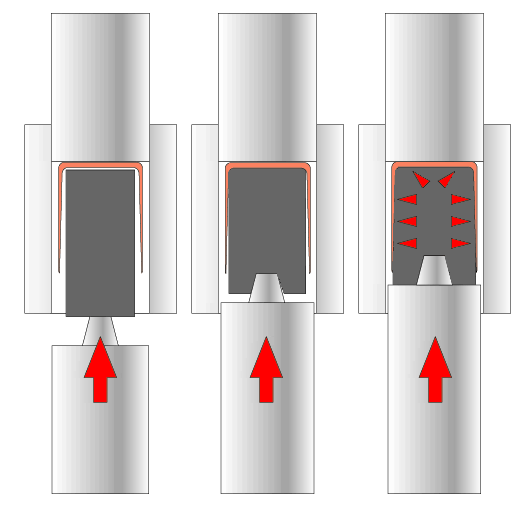
This step is where the core is expanded into the jacket, note that the core when compressed will flow around the punch (and in this case the hollow point is pressed into the lead) until the expansion is stopped by the jacket as it is pressed against the inside of the die.
Note that this punch is made slightly smaller than the inside of the die to fit INTO the jacket to produce a true hollow point with an ogive (curved part of the front) that is covered by the jacket.
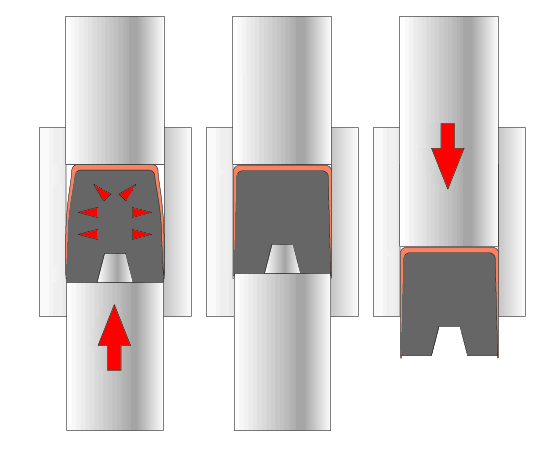
Note that as the punch comes to it's final position the jacket has expanded to the inside of the die with a hard pressed lead core on the inside. As before proper lubrication is necessary or the lead seated into the jacket will lock the jacket into the die, lubrication only on the outside of the jacket.
Once fully seated the jacket and core is ejected from the die.
Fourth step.
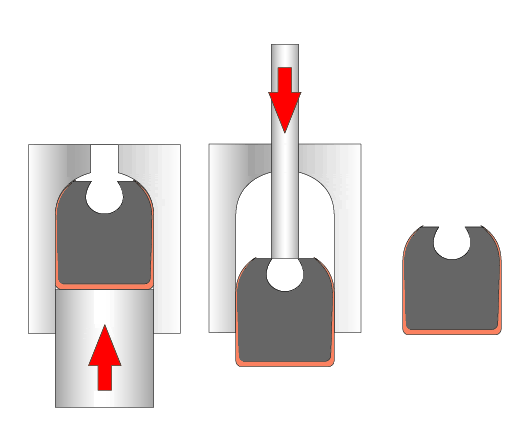
The last step in making this jacketed bullet is to form the point or ogive.
Using the ogive or point forming die, the seated core is placed into the die and will form a point and slightly expand as pressure is applied.
The hollow point is forming under the jacket as the ogive is folded over the open lead.
Once formed the final finished bullet is ejected by a punch.
It takes longer to read that than to do each step...
About the time and force of forming .357 cases and seating a bullet...
For reloading die type swage dies... CH4D
Look under "bullets" from the left hand list...
Go to 101 bullet swage dies...
This is a two step swage die (no core swage) for a jacketed HP...
101410HP 10mm/40 S&W Hollow Point Swaging Die Set - $ 185
Or the soft poont...
101410SP 10mm/40 S&W Soft Point Swaging Die Set - $ 185
The folks at CH4D are great, I have used their "speciality die" custom services before and were great to work with, they make a great product...
The dies they use are the older style Ted Smith type for reloading presses and they can be broken if not uses correctly (in fact all dies can be cracked when using the wrong lead it must be the lead hardness it was designed for harder lead larger holes).
A part of RCE, makes dies for reloading presses...
They also make the special dies for the swage presses (like I use).
I will post more on the CH4D dies and my .355 hollow point set I have.
Thanks for the overview. I've been casting and reloading but only recently ran into swaging when trying to figure out how to deal with undersized 45-70 bullets. Yours is the first explanation that didn't lose me half way.
ReplyDeleteFred
MOLON LABE